Project Detail
Landfill Gas-to-RNG Project
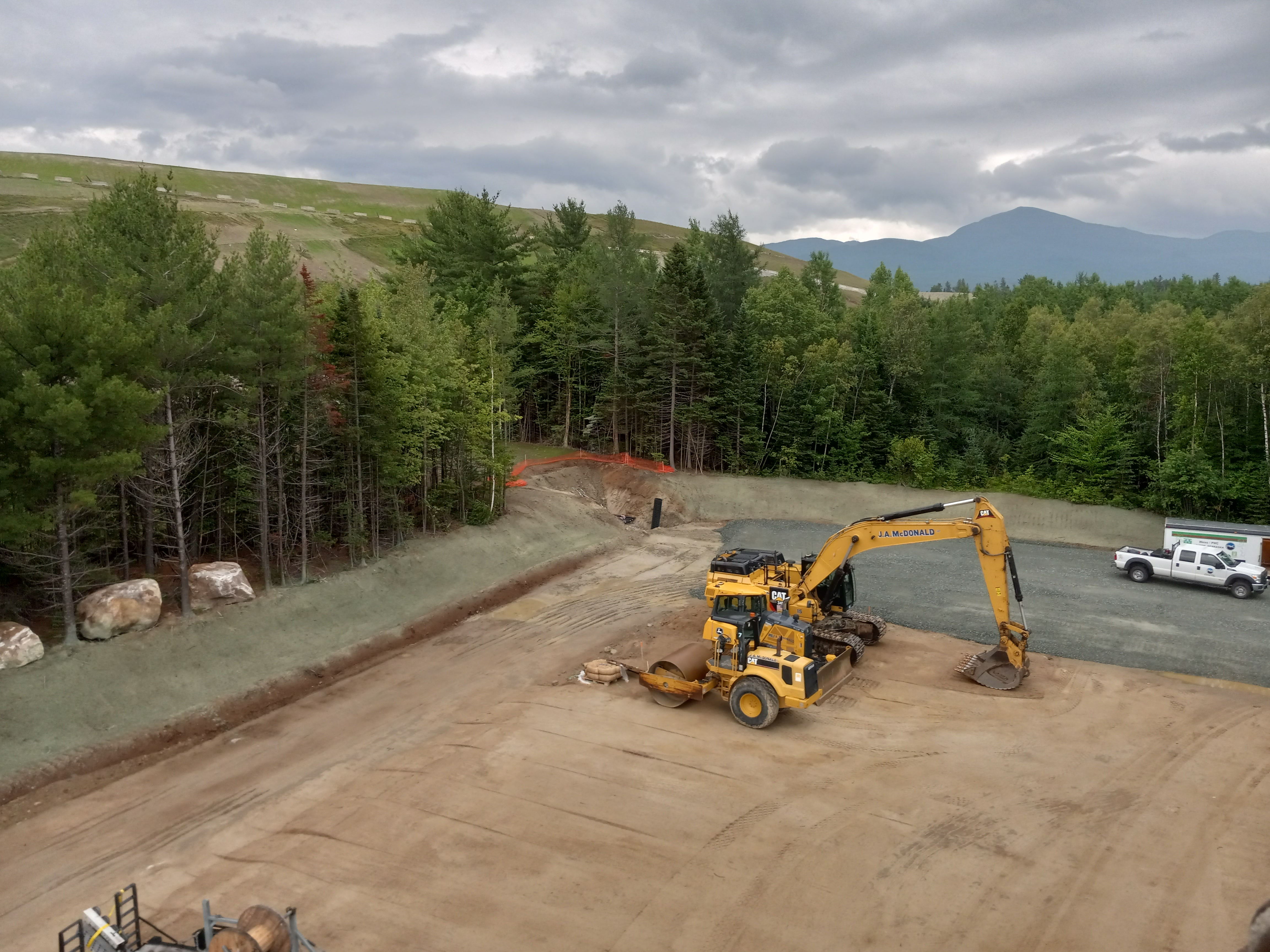
Utilizing the natural byproduct of organic material decomposition led to both financial and environmental benefits for the Bethlehem Landfill. Bartlett & West designed a facility that captures waste gas and converts it to renewable natural gas (RNG). With the addition of an RNG facility, the landfill progressed toward becoming carbon neutral and converting waste into useful biogas.
Challenge
RUDARPA, Inc. constructed a Landfill Gas to RNG facility to upgrade landfill gas to renewable compressed natural gas. They needed third-party engineering support services for the construction phase of the project. Outside expertise was desired to review and comment on Process & Instrumentation Diagrams (P&IDs), Process Flow Diagrams (PFDs) and to ensure continuity between P&IDs from the various project vendors. They also needed an accurate and comprehensive spare parts list, a combined control narrative that accounted for all the Operation and Maintenance (O&M) manuals for the equipment specified. The control narrative was needed to successfully operate the facility. RUDARPA also needed outside expertise to review the HazOp and provide comments.
Solution
Bartlett & West, Inc. and Bartlett & West Operations, LLC provided a thorough site review and office analysis to assure all valves, devices, connections and equipment were in place as detailed in the P&IDs and the PFDs. In addition, marked-up drawings were provided to suggest corrective actions. A review of the confidential HazOp report was undertaken to assure RUDARPA of completeness, systems safety, system operability and compatibility. Where gaps were identified corrective measures were recommended. A site visit was conducted to review punch list items and make recommendations. A facility walk-through report was provided that identified deficiencies and proposed corrective measures.
Value
RUDARPA realized significant confidence in the project, gained control narratives that are still in use today, and was able to work more closely with the contractor and equipment vendors to resolve deficiencies in an expeditious manner saving time during system start up and greatly reducing delays, thereby realizing project revenues sooner. In addition, safety measures and confidence in the overall safety protocol were enhanced.
The dedicated engineering team provided a full suite of services including architectural, site-civil, structural, mechanical, plumbing and process control for ancillary systems. Energy optimization, manufacturers’ equipment drawing oversight and safety equipment design were also included. The scope expanded to include the integration of ancillary controls with vendor-supplied equipment and a safety/trim flare. Additionally, a design was implemented for geothermal heat reutilization in the facility as another method to be more energy-efficient and financially responsible.
Tell us about your project
We’d love to work with you. Tell us the services you are seeking and one of our team members will connect with you.