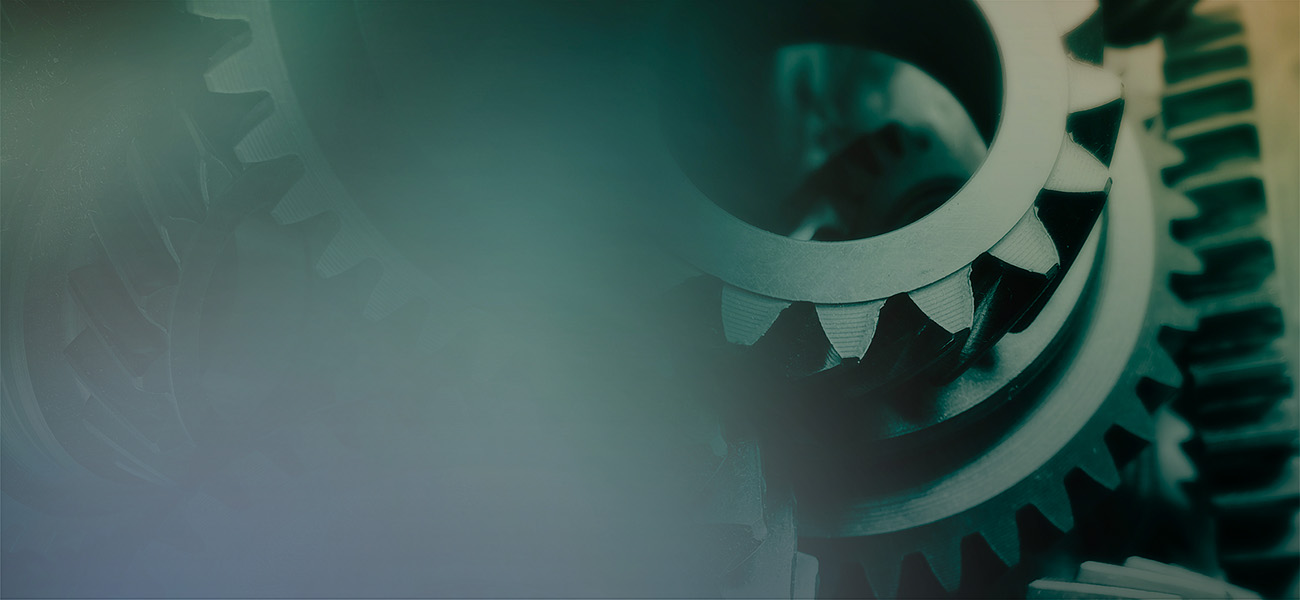
INSIGHT
Best practices to improve safety and profitability of renewable natural gas systems
Connect with us
The design and construction of a new renewable natural gas (RNG) plant or upgrading a current biogas system to pipeline quality RNG, can take months or even years depending on the size and specific requirements of the system.
Once the project is completed, investors and/or taxpayers are anxiously awaiting to see the return on their investment (ROI). While not always a topic thoroughly discussed during the project development process, proper operations and maintenance (O&M) of the plant is essential to maximizing the ROI and plays a large part of the overall success of a project. Advantages include:
- Safer plant environment
- Optimal gas production
- Longer equipment useful life
- Consistent compliance with EPA and other regulatory agencies
- Less downtime, leading to more uptime and more revenue
Plant Safety
To ensure the safety of personnel and plant equipment project owners need to understand the potential risks and establish practical guidelines for accessing and working in the facility. Safety requirements should include:
- Regular assessments of the plant equipment and function should be conducted by trained operators to mitigate any potential risks.
- Regularly calibrate and maintain the gas monitoring equipment throughout the facility. These monitors detect poisonous and explosive gases, which can be odor-less and take only a small amount of exposure to cause serious illness or death.
- As additional precaution, operators and other authorized personnel can wear personal body gas monitors.
- Limit facility access. Only individuals who have been properly trained should be allowed to enter the facilities.
- Training should include how to prevent accidents including static electricity discharge, identification, and correction of leaks.
- Lockout/Tagout
- Confined space entry
- Chemical hazards
- Others
Digester plant safety versus RNG: Addressing concerns from operators
Operators that have been working at a digestion plant may be reluctant to embrace the changes and potential risks with working at an RNG plant. Like biogas, RNG has the potential for explosion, but equipment that compresses the gas in an RNG facility can present added concern. In addition, the new RNG equipment is much more complicated from a technology standpoint and will require operators to learn new processes. Communication and training are key ingredients in getting staff to feel comfortable and buy into the project.
Optimizing Gas Production
The focus of most facilities that have been processing biogas for reuse or sale has been to meet the EPA and pipeline or off-taker requirements, and not on maximizing gas production. It takes having the right equipment and having well-trained and observant facility operators who know what to control to generate more gas. A well-thought-out and utilized maintained program is also a critical factor. No one wants their system to operate at less than its best, but there are numerous factors that can be employed as successful process control strategies that someone with limited time or training may not be aware of. Keeping the plant on-line (uptime) must also be a focus.
Some recommendations and best practices to maximize gas production and reduce costs:
- During the design process work with an experienced company that can recommend the proper equipment to maximize gas production based on the available feedstock.
- Routinely test and analyze substrate throughout the digestion and upgrading process to optimize the mix of feedstock and confirm the system is producing RNG that meets the necessary quality standards.
- Have and use an asset management system that meets or exceeds all manufacturer recommendations.
- A bonus that can be overlooked is the manure or sludge receives better overall treatment, making it more valuable and less costly to then reuse on the farm or in crop production.
Extending Equipment Life
RNG plant equipment is expensive to buy and to maintain. Like optimizing gas production, knowledgeable operators and a complete maintenance approach that is desired to get the most production life from this expensive equipment, is necessary. To keep equipment from failing prematurely, and to help maintain plant safety, we recommend the following:
- Extensive operator training on how to use and maintain the equipment.
- Equipment vendors should provide the training and be able to recommend a supplier who can repair the equipment if a necessary repair is too complex for the operators.
- If you don’t fully understand all the complicated pieces to the puzzle, it is worth partnering with someone who does.
- Follow equipment manufacturers maintenance recommendations.
- Lean on vendors, suppliers, and designers to get what you need and get it when you need it.
- For equipment vital to the operation, keep spare parts on hand to avoid a plant shut down.
- Understand where each single point of failure is and decide if the cost to stock spare equipment is worth it. In many cases, it is.
RNG plants: Hire staff, contractors, or both?
Whether the project is a new RNG facility or an upgrade to an existing facility, additional O&M staff is usually needed. Equipping this staff with exceptional training, resources and access to spare parts is a must if your goal is to maximize uptime and achieve optimal gas production. If you are not able to do that, partner someone who specializes in this.
Municipal Wastewater and Landfill Plants
Depending on the size of the facility it will most likely be necessary to add 1 or more additional staff members. An example based on projects Bartlett & West has completed, plants producing 250 scfm of gas often requires 1½-2 additional skilled operators. Some facilities will also supplement their staff with reputable, experienced contractors on an as-needed basis and to lower the risk of not having redundancy of staff in a key position.
Agriculture Plants
Dairies and other agriculture RNG plants are typically maintained by a team of experienced operator contractors that work in the general geographic area and service several different plants. The team approach helps keep costs down while also enabling rapid response to urgent requests whenever needed.
Staying Compliant
Depending on who is purchasing the gas, different regulations will apply. For instance, if the RNG is being injected into a pipeline and is part of the Renewable Fuel Standard (RFS) program, the EPA has specific requirements the plant must adhere to. If gas is being used locally for vehicle fuel, the regulations may be less strict. Either way, equipment that is operating effectively and is properly calibrated will make reporting requirements easier and help eliminate any variances that could result in fines or public concerns.
Assistance with Planning for O&M
Operating and maintaining an RNG plant is all in the details. Bartlett & West offers a turnkey solution for engineering design, procurement, construction, commissioning and support for the operations and maintenance of RNG projects. Because we have worked on dozens of projects, including dairies, landfills and municipal wastewater, we have a broad range of experience with different equipment manufacturers and know how to assemble a system that maximizes gas production based on a plant’s specific criteria. Our RNG Team has experienced industry veterans to help train operators and provide O&M services in select geographic areas. To learn more fill out the form below to tell us about your project or contact Mark Simms (mark.simms@bartwest.com).
Tell us about your project
We’d love to work with you. Tell us the services you are seeking and one of our team members will connect with you.